Mathey Wireline Unit Manual - The Best Software For Your
THIS AGREEMENT (the Contract), dated effective the day of January 2005, is madebetween:NINOTSMINDA OIL COMPANY (NOC), a Company organised under the laws of Cyprus and having itsregistered office at 22 Stasicratous, Olga court, P.O. Box 48, Nycosia, Cyprus (herein afterreferred as the Operator)SAIPEM S.p.A. Drilling Unit means the land drilling rig IDECO E.
Operator shall have the right at its sole discretion to extend the scope of the Contract in a backto back sequence for up to two additional optional wells, to be located in Georgia, by delivery ofwritten notice to Contractor as follows:First optional well: Operator shall exercise the option to drill the first optional well, as soonas possible and in any case not later than 60 days after the well testing of Firm well has beencompleted. The time from the moment the services are completed on the Firm well ( i.e.
Mast laiddown, mud tanks empty and drilling unit is available to the Contractor for preparing its move)until operation are resumed will be remunerated as per art. If operations under this Contract are suspended for a period of fifteen (15) or more days due toForce Majeure, in which case the demobilisation lump sum fee indicated under Appendix B shall beapplicable; orF. If Contractors Personnel or Drilling Unit do not perform in accordance with internationaloilfield standards for similar services in the reasonable opinion of Operator; orG. If Contractors Drilling Unit does not perform in accordance with manufacturers specificationsfor such Drilling Unit or the specifications set forth in Appendix A in the reasonable opinion ofOperator; orH.
It is understood and agreed that certain personnel of Contractor assigned to the drillingoperations are essential to the operations. Therefore, once the drilling operation has commenced,Contractor shall not transfer any of Contractors Personnel without Operators prior approval.
Contractor shall carry out all operations under this Contract on a day work basis. For thispurpose, the term day work basis means Contractor shall furnish equipment labour and performservices as provided in this Contract, for a specific sum per day under the direction supervisionand control of Operator (which term is deemed to include any employee, agent consultant orsubcontractor engaged by Operator to direct drilling operations). When operating on a day workbasis, Contractor shall be fully paid at the applicable rates of payment and assumes only theobligations and liabilities stated in this Contract. Contractor shall maintain and test its well control equipment listed in the Appendices in goodcondition at all times in accordance with internationally accepted oilfield practices.
Contractorshall use all reasonable means to control wells, to prevent fires and blowouts and to protect thewell during all drilling and completion operations.6) OPERATOR OBLIGATION.6.1) Equipment and PersonnelOperator shall at its cost provide Operators Items and Operators Personnel and perform theservices to be provided by it according to the Contract. Operators Items and Personnel are setforth on Appendices A and D, attached to and made part of this Contract. Operator shall maintainan inventory of Operators Items and keep them available to Contractor to support drillingoperations under this Contract. The drillingsite shall be surveyed and marked by Operator and shall be free of obstructions. 8) RATES OF PAYMENT8.1) PaymentOperator shall pay to Contractor during the term of this Contract the amount from time to time dueat the rates of payment set forth in this Article 8 and in accordance with the other provisions ofthis Contract. No other payment shall be due from Operator unless specifically provided for in thisContract, or agreed to in writing by Operator. The Contractor obtains additional work for the DrillingUnit in direct continuity with the completion of this Contract.8.4) Moving RemunerationThe moving between location shall be remunerated to Contractor in accordance to one of thefollowing options which Operator has to select by giving written notice to Contractor within thirty(30) days from Commencement Date (or in terms of the first optional well within thirty (30) days ofthe spud date of the first optional well).Option 1- Daily rate basisFor the time spent to move the Drilling Unit between locations the Moving Rate shall apply.
TheMoving Rate as detailed in appendix B shall commence when the tree cap is installed and tested, themast laid down, the mud tanks empty and shall cease when Contractor is ready to pick up bit on nextlocation. In the event the moving between location starts following an extended stand by period ofthe Drilling Unit the moving rate shall start when the first load leaves the drilling location.Transportation facilities in addition to those provided by Contractor by the contract, shall befurnished by Operator at its care and charge, or upon Operator request shall be furnished byContractor, and Operator shall reimburse Contractor the relevant documented cost plus theapplicable overhead as per article 6.1.
The Operating Rate indicated under Appendix B will first become payable from the moment when theDrilling Unit spuds the first well at the first drilling location (The bit pass through the rotarytable). The Contract has not beenterminated, subject to termination of the Contract for Force Majeure in accordance with Article2.4(E).8.10) Extended Standby Rate with crew.The Extended Standby Rate indicated under Appendix B shall be payable during the period of any welltest or geological evaluation exceeding seven (7) days and not exceeding sixty (60) days.
Duringthis period the full rig crew and Contractor equipment shall remain at Operator disposal.8.11) Extended Standby Rate Without CrewThe Extended Standby Rate Without Crew indicated under Appendix B will be applicable in caseOperator stops the operation for further geological evaluation up and removes all ContractorPersonnel upon seven (7) days prior notice and not exceeding sixty (60) days. Contractor shallrecommence the operations after Operator gives fifteen (15) days prior notice to Contractor.Operator shall pay Contractor the rates specified in Appendix B per 24 hour days.
Operator willreimburse Contractor transportation costs for returning personnel to their point of origin duringsuch period and again upon returning the personnel to Operating Area immediately prior to there-commencement of Operations.The rate applicable will be an escalating rate. After the first month of application the ratewill be increased by 1.35 times each following month.8.12) Force Majeure Rate Without Crew.The Force Majeure Rate Without Crew indicated under Appendix B will be applicable in case Operatordecides to stop the operation and remove all Contractor Personnel upon seven (7) days prior noticefor reasons of Force Majeure. Contractor shall recommence the operations after Operator givesfifteen (15) days prior notice to Contractor. Operator shall pay Contractor the rates specified inAppendix B per 24 hour days. Operator shall reimburse Contractor transportation costs for returningpersonnel to their point of origin during such period and again upon returning the personnel to theOperating Area immediately prior to the re-commencement of Operations.9) INVOICES AND PAYMENT9.1) Monthly InvoicesContractor shall bill Operator at the end of each month for all daily charges earned by Contractorduring the month.
Other charges shall be billed at the end of the month in which they wereincurred. Billing for daily charges will reflect details of the time spent (calculated to thenearest hour) and the rate charged for the time. Billings for other. Charges will be accompanied byinvoices supporting costs incurred for Operator or other substantiation as required by Operator.9.2) PaymentOperator shall pay by wire transfer all billings within thirty (30) days after the receipt of suchbillings, except that if Operator disputes an item billed, Operator shall within twenty (20) daysafter receipt of the bill notify Contractor of the item disputed, specifying the reason therefore,and payment of the disputed item shall be withheld until settlement of the dispute. Payment shallbe made of any undisputed portion.
If Operator refuses to pay undisputed items, Contractor shallhave the right to terminate this Contract.9.3) Manner of Payment.All payment due by Operator to Contractor under this Contract shall be made in USA Dollars toContractors account to be indicated under Contractors invoices.9.4) Late PaymentIf Operator fails to pay Contractor undisputed amounts invoiced within thirty (30) days afterreceipt of the applicable invoice, Contractor shall be entitled to interest, calculated quarterly,on the undisputed amount remaining unpaid at the London Interbank Offering Rate (LIBOR). Should the drilling activities continue in accordance with art. Of the number of days of use fromcommencement date, the replacement cost and the depreciation value for such equipment.However, Contractor shall be responsible for damages to or loss of Contractor drilling string inthe event its loss, destruction of damage in the borehole is due to Contractor negligence or WilfulMisconduct.10.2) The Hole.Operator shall be solely responsible for damage to or loss of the borehole and other damage belowthe surface, including the casing. If such damage or loss was caused wholly or partially by thenegligence or wilful misconduct of Contractor, its employees, agents or subcontractors, thenContractor shall at Operators direction, drill a new borehole in the same location or re-drillsuch section of the borehole as Operator may require at the Remedial Rate indicated in Appendix B.10.3) Inspection of Materials Furnished by Operator.Contractor agrees to visually inspect all materials furnished by Operator before using suchmaterials and to notify Operator of any apparent defects in such materials.
Not be relieved of anyof its obligations under this Contract both before and after such assignment.Neither Party shall have the right to assign this Contract to any third party without priorapproval of the other Party. And Operators business in the Operating Area.
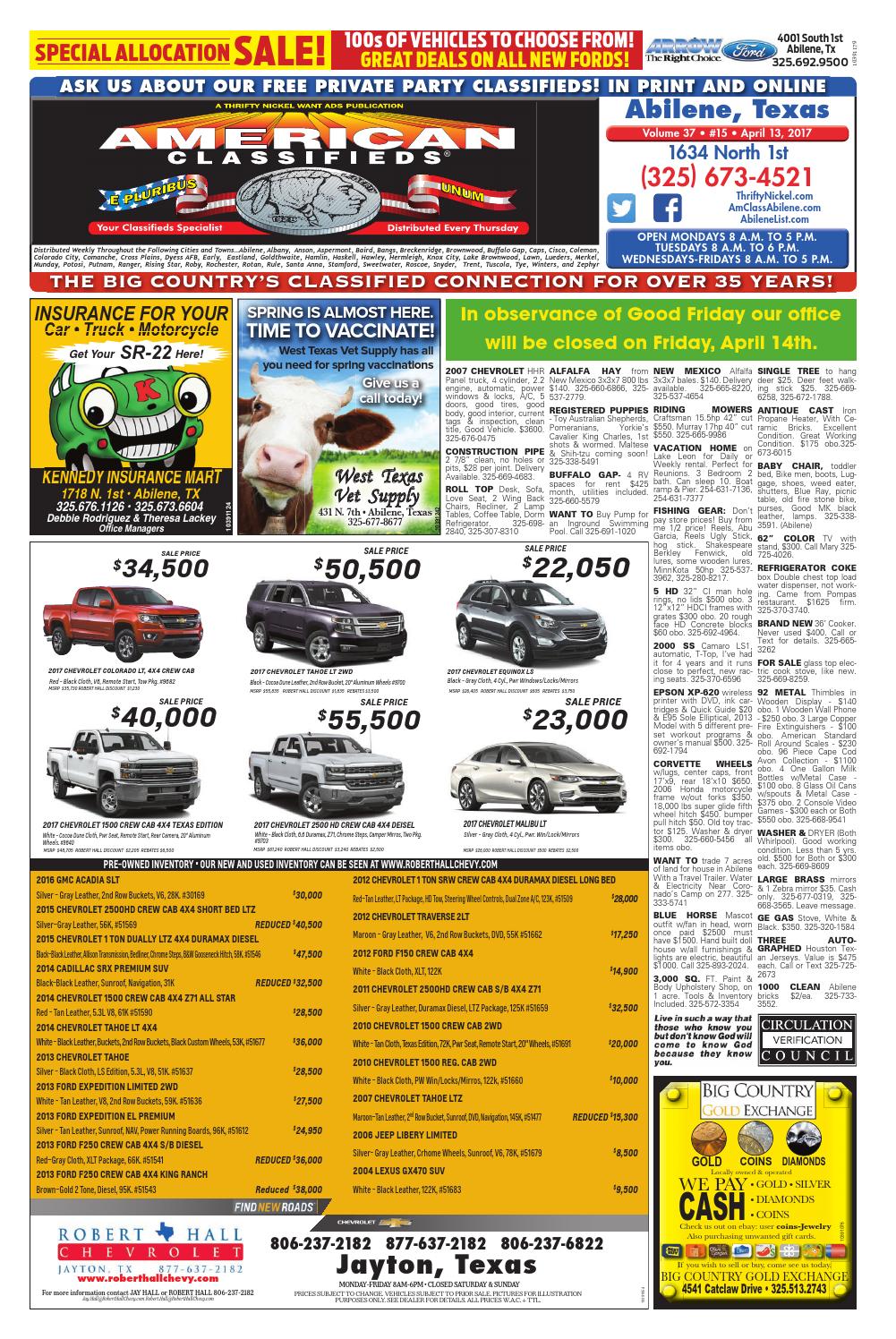
Such Information shall be the sole property ofOperator. Agreed upon by the Parties. Should theParties fail to agree upon a sole arbitrator, then disputes hereunder shall be determined by threearbitrators, one arbitrator being appointed by each Party and the third arbitrator, who will act asChairman, to be appointed by the arbitrators appointed by the Parties. Written agreement of the Parties.14.17) Construction of Ambiguity.The Parties agree and acknowledge that the Contract has been jointly negotiated and drafted andexpresses the mutual intent of the Parties. Accordingly, the rule ofconstruction against the drafting Party, whichever it may be, in the event an ambiguity exists withregard to the interpretation of any particular provision of this Contract shall have no applicationto this Contract.14.18) SuccessionThis Contract shall be binding upon and inure to the benefit of the Parties and, subject to theterms of this Contract, their respective successors and permitted assigns.IN WITNESS WHEREOF, the duly authorised representatives of the Parties have executed this Contractin two originals the date shown below. Verified and tested during such time. All valves shouldbe tested to confirm free of leaks. 2.2 Operate and function test the vacuum degasser.
Verify vacuum pressure is to specification. 2.3 Operate and function test shakers with water. 2.4 Operate and function desilter, mud-cleaners and desander. Check that suction and dischargelines are correctly positioned. Note that screens of mud-cleaners and/or shakers maydeteriorate with excessive testing with water alone. Limit test duration for such equipment. 2.5 Function test agitators and mud guns in all equipped tank. Function and verify transferoptions between tanks. Verify that mud tank measuring and gain/loss equipment is operatingcorrectly and has been correctly calibrated. Check tank measuring devices such that they arecorrectly calibrated.
Verify diesel supply lines, rates of supply and transfer optionsbetween tanks. Check that a volumetric counter is available and that it is correctlycalibrated. 3.0 Bulking Plant (if supplied) 3.1 Test air lines and valves.
Cambridge academic english c1 advanced teacher's book pdf. Cambridge Academic English C1 Advanced Student's Book).pdf - Free ebook download as PDF File (.pdf) or read book online for free.
Check for leaks. 3.2 Test silos at their rated pressures with air. 3.3 Using 15 tones of Barytes function transfers from silo to silo Check load cell calibration,time for transfer and amount of barytes left untransferred by the end of the test. 4.0 Blow Out-Preventers and Well Control Equipment 4.1 Each preventer unit shall be function tested and times, pressure and volumes of controlfluid required recorded. Function tests will be carried out from the BOP control unit,Drillers remote panel and other remote panel (if any) for each preventer and hydraulicallycontrolled valve. 4.2 Each preventer will be pressure tested for fifteen(15) minutes with water.Test should be carried out at low pressure for five (5) minutes and ten (10) minutes atthe rated pressure. 4.3 Fill the trip tank and check the calibration. Check the operation of fill-up pump, valvingand dump valve.
5.0 BOP Control Unit 5.1 Following verification of pre-charge pressure the BOP control unit will be charged to itsworking pressure utilising air and electric pumps. The time taken to reach working pressureshall be noted and recorded and confirmed within specification. The control unit will thenbe purged to its pre-charge pressure and then, using the electric pump or pumps only,charged to its working pressure and the time taken noted and recorded and confirmed withinspecification. The control unit will then be purged again to its pre-chare pressure andthen, using the air pump or pumps only, charged to its working pressure and the time takennoted and recorded and confirmed within specification. 5.2 Place a pup-joint across the annular preventer and disconnect the air and electric chargepumps.
Observe and record the pressure in the control unit. Close all the preventerssequentially in the stack noting and recording the times for each preventer to close and thequantity of hydraulic fluid used to operate the closing of each preventer. Note and recordresidual pressures in the control unit and confirmed these with manufactures performancecharacteristics. Re-connect the air and electric pumps and recharge the unit to its working pressure.
Noteand record the time taken for the unit to achieve its working pressure. Note and recordthe pressures at which the pumps stop and start. 6.0 Hoist and Mast Equipment 6.1 Hoist will be worked, without load, at each speed. 6.2 Catheads will be functioned and oil and air pressures checked and calibrated. Torquemeasuring equipment will be checked and calibrated. 6.3 Check auxiliary brake and crown block protection device. 6.4 Check all measuring devices and calibrate if necessary. 6.5 Operate the stabbing board. 7.0 Rotary Table 7.1 Operate the rotary table for one (1) hour under no load at various speeds. Check the rotary lock. Calibrate the rotary torque measurement device and the rotary speed counter. 8.0 Equipment and Spare Part Inventory 8.1 A full inventory of the contractual list of equipment will be taken and verified byOPERATORs representative with the aid of CONTRACTORs representative. 8.2 CONTRACTORs inventory of spare parts will be inspected by OPERATORs representative. 9.0 Certification 9.1 Availability of Inspection certificates for downhole and major hoisting equipment. (Issuing Bank: H.S.B.C)(Advising Bank: H.S.B.C. Milan Branch)RE: OUR IRREVOCABLE STAND - BY LETTER OF CREDIT N°. By order and for the account of.- hereafter referred to as COMPANY, we issue anIrrevocable Stand - By Letter of Credit N°.
In favour of SAIPEM S.P.A.Via Martiri diCefalonia, 67 - San Donato Mil.se, Milano, Italy-, hereafter referred to as Saipem for the amountof USD 1,100,000 (One Million and one hundred thousand United States Dollars).The validity of this Stand - By Letter of Credit is up toJuly 15 th, 2005.Funds under this credit will be available to you on first demand upon our receipt of the followingdocuments:a) Your original statement purpotedly signed by an authorized representative of Saipem statingCOMPANY has failed to comply with the payment conditions of the drilling contract dated. WithSaipem S.p.A., therefore we draw USD 1,100,000 under Stand-By letter of credit n°. Issued inour favor by Issuing bank ;b) Copy of invoice issued to COMPANY for mobilisation services rendered under the DrillingContract dated.between Saipem and COMPANY.Reference to the drilling contract is for information purposes only and its terms and conditionsare not incorporated in this Stand-By letter of credit. Partial drawings are not permitted.This credit is not transferable. Credit and rights under this Standby Letter of Credit shall not beassigned.
IRREVOCABLE STAND - BY LETTER OF CREDIT FORMAT 2 (Issuing Bank: H.S.B.C.)(Advising Bank: H.S.B.C. Milan Branch)RE: OUR IRREVOCABLE STAND - BY LETTER OF CREDIT No. By order and for the account of.- hereafter referred to as COMPANY, we issue anIrrevocable Stand - By Letter of Credit N°. In favour of SAIPEM S.P.A.Via Martiri diCefalonia, 67 - San Donato Mil.se, Milano, Italy-, hereafter referred to as Saipem up to Amountof USD 2,250,000 (Two Millions and two hundred and fifty thousandUnited States Dollars).The validity of this Stand - By Letter of Credit is up toOctober 30 th, 2005.Funds under this credit will be available to you on first demand upon our receipt of the followingdocuments:a) Your original statement purpotedly signed by an authorized representative of Saipem statingCOMPANY has failed to comply with the payment conditions of the drilling contract dated. WithSaipem S.p.A., therefore we draw up to Amount of USD 2,250,000 (Two Millions and two hundred andfifty thousand United States Dollars) under Stand-By letter of credit n°. Issued in our favorby Issuing bank;b) Copy of invoice(s) issued to COMPANY for drilling services rendered under Contract dated.between Saipem and COMPANY.
Reference to the drilling contract is for information purposes only and its terms and conditionsare not incorporated in this letter of credit.Partial drawings are permitted.The total amount of this Standby Letter of Credit shall be reducedaccordingly to reflect the partial drawings if any.This credit is not transferable.Credit and rights under this Standby Letter of Credit shall not beassigned. IRREVOCABLE STAND - BY LETTER OF CREDIT FORMAT 3 (Issuing Bank:H.S.B.C.)(Advising Bank: H.S.B.C. Milan Branch)RE: OUR IRREVOCABLE STAND - BY LETTER OF CREDIT No. By order and for the account of.- hereafter referred to as COMPANY, we issue anIrrevocable Stand - By Letter of Credit N°. In favour of SAIPEM S.P.A.Via Martiri diCefalonia, 67 - San Donato Mil.se Milano, Italy-, hereafter referred to as Saipem for the amountof USD 550.000,00 (Five hundred and fifty Thousand United StatesDollars).The validity of this Stand - By Letter of Credit is up toDecember 30 th, 2005.Funds under this credit will be available to you on first demand upon our receipt of the followingdocuments:a) Your original statement purpotedly signed by an authorized representative of Saipem statingCOMPANY has failed to comply with the payment conditions of the drilling contract dated. WithSaipem S.p.A., therefore we draw USD 550,000 under Stand-By letter of credit n°. Issued in ourfavor by Issuing bank ;b) Copy of invoice issued to COMPANY for demobilisation services rendered under the DrillingContract dated. Between Saipem and COMPANY.
Reference to the drilling contract is for information purposes only and its terms and conditionsare not incorporated in this Stand-by letter of credit.Partial drawings are not permitted.This credit is not transferable. Credit and rights under this Standby Letter of Credit shall not beassigned.
Now that you are well on your way to developing your content for your policy and procedure manual, it is time to consider the format.Even though your manual will have valuable information, it will not benefit your staff if no one reads it. How can you design and format the manual so that it is easy to read and digest?In this article, we will consider the appearance of your manual. It is critical that you pay attention to how the manual looks to the reader, because its appearance reflects the professionalism of your company.Key elements to consider are:OrganizationClear headingsAppropriate text sizesWhite spaceVisual elementsPaper qualityCover and bindingOnline version, electronic distributionOrganization. Some of your favorite novels and movies might start in the middle and switch back and forth from the past to the present.
While those changes in time may be effective in fiction, they will not work with your policy and procedure manual.A typical printed manual has a cover, a title page, a foreword or introduction, the Table of Contents, the policies and procedures, and index.Use your Table of Contents as your guide to organizing your main information. Number your policies and procedures for easy reference. Both your main sections and any sub-sections should be numbered.You can number your sub-sections with a decimal format.Section 1. Safety and Health1.1 Emergency preparedness1.2 Personal hygiene1.3 Equipment cleaningAnother important means of organizing your manual is to number your pages. All business documents that are more than a few pages long should have page numbers.
When you link your table of contents with those page numbers, your readers will be able to find what they are looking for.Remember that these page numbers will change as you finalize your document, and again when you make revisions later.HeadingsThe headings for each section should clearly state the procedure or policy it contains. The wording should make it easy for an employee to find that information.
For instance, if a worker is seeking information on the dress code, your workplace policy should be filed under the heading 'Dress Code.' If other terms are often used in your company for work clothes, such as the word 'uniform,' you can also use that word in your index to direct readers to the 'Dress Code' section.The sub-sections in your policies and procedures should also have clear headings. For example, your 'Personal Electronics' section may contain subsections called 'Texting' and 'Social Media.' Use your Table of Contents to outline your guide, and to make sure that all appropriate policies and procedures are covered in your manual. In addition to making your manual easy to read, this outline format will also make it easy for you to make updates and revisions to your manual, as they are needed.Text sizesChoose a type style and a font size that is easy to read. Times New Roman and Calibri are two standard choices. The common font size used for body text is 10- or 12-point.
Use a font size two sizes larger for headings. It helps the reader, if you also put headings in bold face. You may choose to put Policy titles in all caps and bold, and sub-sections in upper and lower case and bold.
Interested in learning more? Why not take an?Here is an example:SECTION 1 HEALTH AND SAFETY1.1 Personal SafetyXYZ puts safety first.
We go above and beyond OSHA regulations by.1.2 Equipment SafetyWhite SpaceNo one likes to look at large blocks of gray text. To avoid this problem, leave plenty of white space around your text and your headings.White space, sometimes called negative space, is the space between elements in a report or manual. White space increases legibility.
Legibility increases comprehension. According to a study conducted on readability, the effective use of white space can increase readability by 20 percent (Sillence, Briggs, Fishwick and Harris, 2004).Aim to make your margins at least one inch from each side of the pages of your manual.
Also, allow space between your headings and your copy or graphic elements. This space helps headings stand out from the other elements on the page.You can add white space to your document by using bulleted and numbered lists.Visual elementsNow, it's time to think about ways you can make your manual more visually appealing by using any graphic elements. Charts, diagrams, and photos can help convey your meaning and provide interest.For example, an organizational chart, such as the one below, may be very helpful for new employees. Be sure to give the text plenty of white space in the box.
Otherwise, it may look crowded and uninviting, defeating the purpose of the box altogether.Color is another way you can add interest to your manual. Adding a color to your headlines or certain graphic elements can work well.
According to research by McGraw-Hill, color in business documents increases readership by 40 percent, and can increase the retention of material by 18 percent.Just be careful not to overdo. Too much color can take away from the professionalism of your material.
In addition, certain colors, such as yellows and pinks, do not provide enough contrast on the page and, as a result, are hard to read.Paper qualityIf you are supplying print copies of your manual to your employees, this is not the time to scrimp on quality.If you expect the manual to be read once and discarded, thin paper is acceptable. However, if you expect your employees to keep this manual and refer to it often, then you will want to use high quality paper for printing.Business papers, printer papers, and personal stationery range usually in weight from 20-pound to 32-pound. The most common paperweight is 20-pound.
What Is The Best Software
Cover and bindingSince your manual's content is likely to change periodically as you revise and update information for your organization, a three-ring binder is a good choice. Tabbed subject inserts can allow for quick and efficient indexing.If your manual has a very low page count, say eight pages, you may do well with plastic folders that are three-pronged or have a slide-on plastic spine.Another option is to have a printer bind your manual. If your manual is 64 pages or less, a simple saddle stitch binding will work well. Talk with your printer about your options.The front cover and back cover should be of a durable weight in order to withstand frequent use.
Many printed manuals have a thick, coated paper cover and are bound with what is known in the printing industry as 'perfect' binding. In perfect binding, the manual has a soft cover, and the pages are held together with the use of flexible glue on the spine.For longer manuals, the pages can be stitched together for added reinforcement, before the glue is applied. If you would like the manual to lie flat when it is open, you may opt for a plastic comb, or a spiral binding.Online version, electronic distributionStrictly web-based manuals cost less to establish and to maintain. However, there is something official and professional about presenting your staff with a printed manual.Many companies choose to have both a paper version of their manual and an electronic version. They can make revisions to the printed manual and simply notify employees when those additional or corrected pages are available online.These notifications can instruct employees to print out the new pages to add to their existing manual.Depending on your organization, you may wish to include some supplementary sections at the end of your manual. One such section is a glossary. The glossary will include terms and their definitions and common industry abbreviations that new employees may need to learn.Place your glossary terms in bold, followed by the definition in regular text format.
Alphabetical order will help you readers be able to quickly scan the list for the item they are looking for.Here is an example of a few glossary entries for a financial firm.Accounts Payable – debts incurred during daily operations.Accounts Receivable - monies due as the result of daily operations.Assets - all real or intellectual property that has a positive financial value for the company.Balance Sheet - a statement of the company's assets and liabilities.You can put the glossary section at the end of your manual. Another option is to include a numbered definition sub-section in each section of the manual, as needed. Another section you may wish to include at the end of your manual is a compliance page. This page could include a general statement about how policies are enforced, and a description about the consequences of violating company policy.As with the glossary, you may choose to include this information at the end of each policy, instead of having this in a separate section.Many policy and procedure manuals include a removable section at the end for the reader to sign and date. This page serves as proof that employees have read and agreed to abide by the policies and procedures contained in the document.A word about lengthAmerican Founding Father Thomas Jefferson is credited with advising writers and speakers, alike, to never use two words when one will do. This is a rule to keep in mind with all your business writing, including your policy and procedure manual.In the previous chapter, we discussed how polices and procedure should be written with clarity and conciseness in mind.
As a general benchmark, aim to keep each policy no longer than one page.This brevity will give natural breaks to the format of your manual.Be aware of awkward page breaks as you finalize your document. Avoid having single words or single lines at the top of a page or column.It looks better to have at least two lines of a paragraph at the top of a page. Also, avoid the placement of a heading as the last line of a page. A heading should have at least two lines following it - and more, in the case of major headings.Try not to break up short lists between pages as well. If the list has six or fewer lines, start the whole list on the next page to assure better readability.Now, let's look at some formatting issues that may pertain to nonprofit organizations.Your nonprofit's policy and procedure manual will need to include specific language and policies relevant to the workings of a nonprofit organization. Additional sections may be needed that are dedicated to the elections and operation of the board of directors and the board committees.You may wish to include specific policies on how board members are to carry out their duties.
In addition, the duties, powers, policies, and procedures of ongoing and ad hoc committees can be detailed in your policy manual.Printed copies of this manual can be prepared before the annual board meeting, and distributed to all new board members upon their election, or at their orientation sessions. The Wallace Foundation, a nonprofit association that provides resources and assistance to the management of nonprofit organizations, offers this link to help nonprofits with developing a policy and procedure handbook.